INTERVIEW
先輩社員インタビュー
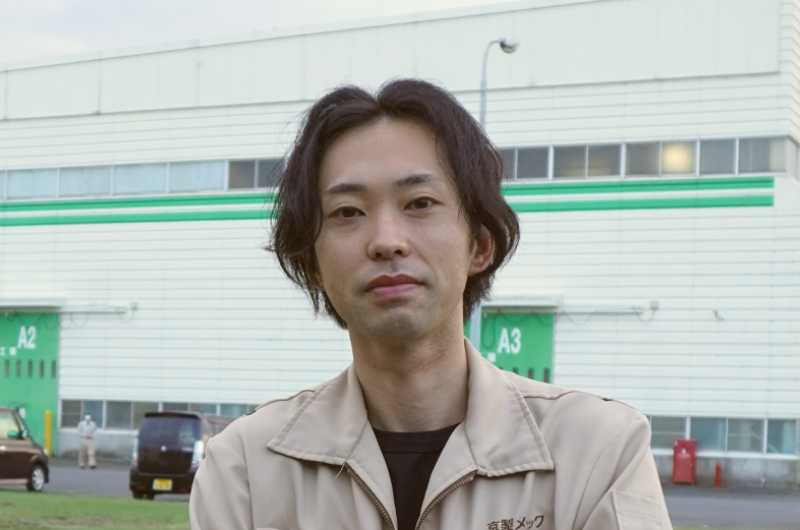
機械に完成はない。「常に疑問を持つ」ことが大事
技術部 機械設計
大分大学大学院 機械・エネルギー工学専攻
機械コース修了
2017年入社
入社3年目に難しい課題にチャレンジ。
京製メックは「やりたい」と手を上げた社員に、社歴や年齢に関係なくどんどん仕事を任せてくれる会社です。逆に手を上げないと、なかなか面白い仕事に巡り会えません。
私が「それ、やらせてください」と立候補したのは某製薬メーカーで使われる「横型カートナー+圧着検査装置」という機械の設計でした。「カートナー」とは箱の中に製品を詰める機械です。今回の場合、錠剤が1シートあたり、10錠入ったものを10シート重ね、袋に詰められたものを説明書と一緒に箱の中に入れ糊で閉じます。また、圧着検査装置とはカートナーでつくられた箱がしっかりと糊付けされているか検査する装置です。機械としてはそれほど難しくないのですが、工場のレイアウトの関係で「圧着検査装置」に大きなスペースを取れないというのが大きな課題でした。いま思えば、よく3年目の社員に任せたなという感じです。
本当は2メートルくらいのスペースが必要。
圧着検査は糊づけされた取り出し口に引っ張る力を加え、それをセンサーで測定するという仕組みです。医薬品の小箱を右から左へ直線的に流しながら検査するとしたら、2メートルくらいの設置スペースが欲しいところです。ですが与えられたスペースはその半分の1メートル。しかも「カートナー」は1秒に1個というスピードで箱詰め・糊づけをするので、「圧着検査装置」も同じ速さで稼働させないといけません。
私が担当したのは、この検査装置のメカ設計。つまり機構を考える工程です。ただ経験の浅い私がまったく一人でやるのは困難でした。会社は「手を上げた者に任せる」という方針ですが、いつもベテランの先輩が近くにいて「何でもすぐに聞ける環境」でもあります。なのでいろいろな先輩に相談しながら、試行錯誤を繰り返しました。
あえて「必要な部分を取り除く」挑戦。
悩んだ末に考えついたのは2つの挑戦です。
1つ目は本来ならばカートナーから出てきた箱を圧着検査装置に送り込む際、つかんで移動させる機構が必要なところを、あえてその機構を取り除き直接飛び込んでも大丈夫な設計に挑戦しました。
2つ目は圧着検査装置の出口部分です。これも同じようにつかんで移動させる機構が必要でしたが、この部分を取り除く挑戦をしました。しかし、この機構を取り外すと試行錯誤しても不具合が出てしまい、取り除くことはできなかったので出口から出てきたカートンを横に移動させるのではなく、直角方向に移動させ奥行きを使うことにより省スペース化に成功しました。
さらには必要最低限のシンプルな設計にすることで、メンテナンス性、アクセス性の向上を図り、将来違う品種を生産することになっても対応できるようにしました。
結果、お客様からも高評価をいただき、リピート機のご発注をいただくことができました。自分の設計が評価され、会社の売上にも貢献できたわけですから、このときは本当に嬉しかったですね。ただリピート機といっても、京製メックではまったく同じ機械をもう一台納品するということは絶対にしません。
「常に疑問を持て」が社長の教えだから。
たとえ機械に問題がなくても、お客様からの要望がなくても、次に納品する一台には必ず手を加えます。まったく同じ物は作らないというのが会社の方針ですし、胸には「常に疑問を持て」という社長の言葉が染み込んでいますから。
もしかしたら改良したことをお客様に気づいてもらえないかもしれません。でも「あれ、ここ見やすくなってる」「前より製品を手に取りやすくないか」と気づいてもらえたら、「さすが京製メックさん、気が利くね」となり、信頼が深まります。私も機械には「これで完成」というゴールはなく、いくらでも「より良くする」余地があると思っています。リピートいただいた「圧着検査装置」に次はどんな工夫を加えようか、いまワクワクしながら考えているところです。
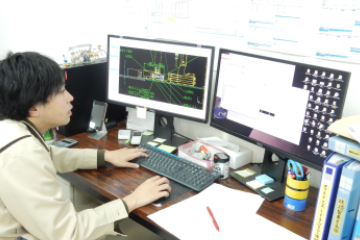
私が「それ、やらせてください」と立候補したのは某製薬メーカーで使われる「横型カートナー+圧着検査装置」という機械の設計でした。「カートナー」とは箱の中に製品を詰める機械です。今回の場合、錠剤が1シートあたり、10錠入ったものを10シート重ね、袋に詰められたものを説明書と一緒に箱の中に入れ糊で閉じます。また、圧着検査装置とはカートナーでつくられた箱がしっかりと糊付けされているか検査する装置です。機械としてはそれほど難しくないのですが、工場のレイアウトの関係で「圧着検査装置」に大きなスペースを取れないというのが大きな課題でした。いま思えば、よく3年目の社員に任せたなという感じです。
本当は2メートルくらいのスペースが必要。
圧着検査は糊づけされた取り出し口に引っ張る力を加え、それをセンサーで測定するという仕組みです。医薬品の小箱を右から左へ直線的に流しながら検査するとしたら、2メートルくらいの設置スペースが欲しいところです。ですが与えられたスペースはその半分の1メートル。しかも「カートナー」は1秒に1個というスピードで箱詰め・糊づけをするので、「圧着検査装置」も同じ速さで稼働させないといけません。
私が担当したのは、この検査装置のメカ設計。つまり機構を考える工程です。ただ経験の浅い私がまったく一人でやるのは困難でした。会社は「手を上げた者に任せる」という方針ですが、いつもベテランの先輩が近くにいて「何でもすぐに聞ける環境」でもあります。なのでいろいろな先輩に相談しながら、試行錯誤を繰り返しました。
あえて「必要な部分を取り除く」挑戦。

1つ目は本来ならばカートナーから出てきた箱を圧着検査装置に送り込む際、つかんで移動させる機構が必要なところを、あえてその機構を取り除き直接飛び込んでも大丈夫な設計に挑戦しました。
2つ目は圧着検査装置の出口部分です。これも同じようにつかんで移動させる機構が必要でしたが、この部分を取り除く挑戦をしました。しかし、この機構を取り外すと試行錯誤しても不具合が出てしまい、取り除くことはできなかったので出口から出てきたカートンを横に移動させるのではなく、直角方向に移動させ奥行きを使うことにより省スペース化に成功しました。
さらには必要最低限のシンプルな設計にすることで、メンテナンス性、アクセス性の向上を図り、将来違う品種を生産することになっても対応できるようにしました。
結果、お客様からも高評価をいただき、リピート機のご発注をいただくことができました。自分の設計が評価され、会社の売上にも貢献できたわけですから、このときは本当に嬉しかったですね。ただリピート機といっても、京製メックではまったく同じ機械をもう一台納品するということは絶対にしません。
「常に疑問を持て」が社長の教えだから。
たとえ機械に問題がなくても、お客様からの要望がなくても、次に納品する一台には必ず手を加えます。まったく同じ物は作らないというのが会社の方針ですし、胸には「常に疑問を持て」という社長の言葉が染み込んでいますから。
もしかしたら改良したことをお客様に気づいてもらえないかもしれません。でも「あれ、ここ見やすくなってる」「前より製品を手に取りやすくないか」と気づいてもらえたら、「さすが京製メックさん、気が利くね」となり、信頼が深まります。私も機械には「これで完成」というゴールはなく、いくらでも「より良くする」余地があると思っています。リピートいただいた「圧着検査装置」に次はどんな工夫を加えようか、いまワクワクしながら考えているところです。