INTERVIEW
先輩社員インタビュー
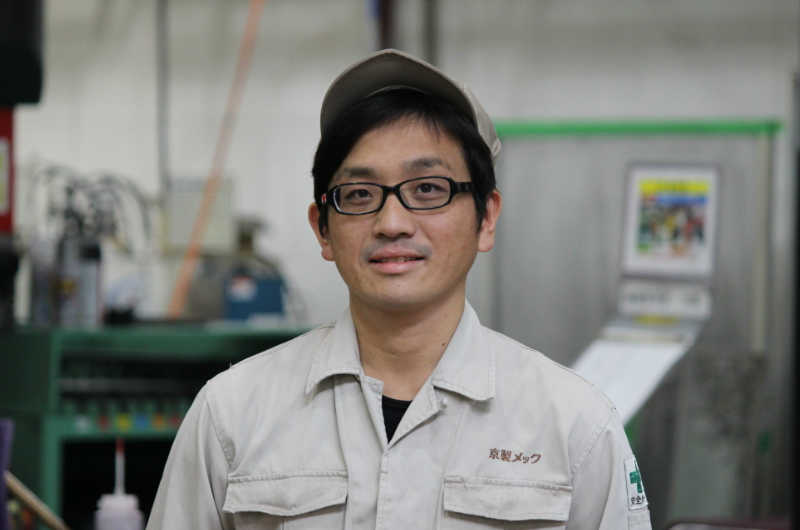
ひとつの部品が機械の性能やコストを左右するんです
工作部 板金課
大分県立工科短期大学 生産技術科 卒
2005年入社
大分県立工科短期大学 生産技術科 卒
2005年入社
部品から自社で作る会社は少ないと思う。
京製メックは機械の設計、加工・組立てをすべて自社で行います。さらに部品の多くも自社で作りますので、まさに「一台一台を手作り」という感じですね。ここまで自社製作にこだわる会社は少ないかもしれません。
実は私も「すべての工程に携わるチャンスがある」という点に惹かれて入社。以来、主に部品加工に携わってきました。最初の5年ほどは「MC(マシニングセンタ)課」で、金属の塊から部品を削り出すという仕事。
その後は「板金課」に移り、いまは精密溶接などを行いながら、課をまとめたり、後輩を指導したりという役割を担っています。
部品を作る「治具」まで作ってしまう。
ちょうど板金課に移るころ、レーザー加工機が導入されました。それを見た私は「これまでMCで加工していた角パイプをレーザーで切断できないか」と思ったのです。
角パイプは機械の土台を支えるのに不可欠な部品。しかも機械の大きさ、設置場所などによって強度・長さが異なり、加工する数も多い。これをレーザーでやれば時間もコストも削減できると考えました。苦労したのは角パイプを固定する方法。最初は万力のような仕組みでネジを締めて固定しました。しかしこれでは着脱に時間がかかり、人によって締める力も違ってきます。次にマグネットを試しましたが、今度は固定する力が不足。そこで思いついたのがエアシリンダでの固定です。これなら着脱も一瞬で、加える力も一定に保てます。
仲間と試行錯誤しながら完成させた「固定用の治具」は、いまも毎年改良を加えながら大活躍中。そして実際、時間やコストの抑制に大きく貢献しています。
精密溶接で設計者の構想を実現する。
部品加工は「図面どおりに部品を作るだけ」と思われがちですが、決してそうではありません。
加工者という立場から、設計者に対して様々な提案やアイデア出しを行います。そして同時に高い技術で設計者の構想を実現させます。例えば、コストのかかる部品の場合「この材料なら同じ強度でコストを抑えられる」と提案したりします。また私たちの精密溶接の技術も機械作りには欠かせません。熱によってすぐ曲がったり歪んだりする厚さ0.5mmほどのステンレス板を、変形させず正確に溶接する技術は習得に5年ほどかかります。この精密溶接ができるかどうかで、機械の機能・性能も変わってきます。時には設計者から「ここ何とか溶接できませんか」といった相談を受けることも。設計・部品加工・組立てなど多くの技術者が力を合わせて、初めて一台の機械が完成します。
学生時代に学んだことが必ず役に立つ。
私は大学で製図・プログラミング・加工技術・材料力学など、いろんなことを学びました。そしていま「学んだことすべてが役立っている」と実感しています。
もちろん入社後すぐに活かせるわけではありません。ただ数年経って何かの課題にぶつかったとき、「あっ、これはあのころ勉強したな」と思い出すことが多々あります。例えば角パイプのレーザー加工は様々な加工技術を学んでいたから生まれた発想ですし、材料力学の知識がなければ設計者に強度のアドバイスをすることもできません。
機械のすべてを手作りしているから、学生時代に何を学んでいても必ずそれを発揮できる場面がある。京製メックは、そんな会社だと思います。
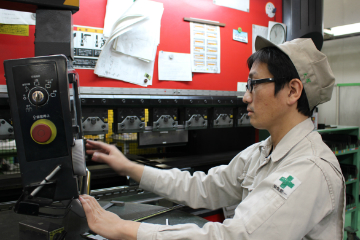
実は私も「すべての工程に携わるチャンスがある」という点に惹かれて入社。以来、主に部品加工に携わってきました。最初の5年ほどは「MC(マシニングセンタ)課」で、金属の塊から部品を削り出すという仕事。
その後は「板金課」に移り、いまは精密溶接などを行いながら、課をまとめたり、後輩を指導したりという役割を担っています。
部品を作る「治具」まで作ってしまう。
ちょうど板金課に移るころ、レーザー加工機が導入されました。それを見た私は「これまでMCで加工していた角パイプをレーザーで切断できないか」と思ったのです。
角パイプは機械の土台を支えるのに不可欠な部品。しかも機械の大きさ、設置場所などによって強度・長さが異なり、加工する数も多い。これをレーザーでやれば時間もコストも削減できると考えました。苦労したのは角パイプを固定する方法。最初は万力のような仕組みでネジを締めて固定しました。しかしこれでは着脱に時間がかかり、人によって締める力も違ってきます。次にマグネットを試しましたが、今度は固定する力が不足。そこで思いついたのがエアシリンダでの固定です。これなら着脱も一瞬で、加える力も一定に保てます。
仲間と試行錯誤しながら完成させた「固定用の治具」は、いまも毎年改良を加えながら大活躍中。そして実際、時間やコストの抑制に大きく貢献しています。
精密溶接で設計者の構想を実現する。
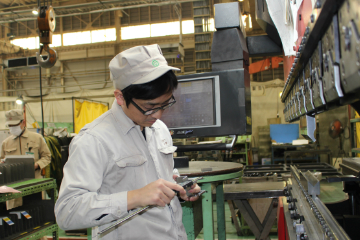
加工者という立場から、設計者に対して様々な提案やアイデア出しを行います。そして同時に高い技術で設計者の構想を実現させます。例えば、コストのかかる部品の場合「この材料なら同じ強度でコストを抑えられる」と提案したりします。また私たちの精密溶接の技術も機械作りには欠かせません。熱によってすぐ曲がったり歪んだりする厚さ0.5mmほどのステンレス板を、変形させず正確に溶接する技術は習得に5年ほどかかります。この精密溶接ができるかどうかで、機械の機能・性能も変わってきます。時には設計者から「ここ何とか溶接できませんか」といった相談を受けることも。設計・部品加工・組立てなど多くの技術者が力を合わせて、初めて一台の機械が完成します。
学生時代に学んだことが必ず役に立つ。
私は大学で製図・プログラミング・加工技術・材料力学など、いろんなことを学びました。そしていま「学んだことすべてが役立っている」と実感しています。
もちろん入社後すぐに活かせるわけではありません。ただ数年経って何かの課題にぶつかったとき、「あっ、これはあのころ勉強したな」と思い出すことが多々あります。例えば角パイプのレーザー加工は様々な加工技術を学んでいたから生まれた発想ですし、材料力学の知識がなければ設計者に強度のアドバイスをすることもできません。
機械のすべてを手作りしているから、学生時代に何を学んでいても必ずそれを発揮できる場面がある。京製メックは、そんな会社だと思います。